測力傳感器的使用壽命受多種因素影響,通常從數年到數十年不等,具體取決于設計質量、使用環境、負載類型及維護水平。以下是影響測力傳感器壽命的關鍵因素及延長使用壽命的策略:
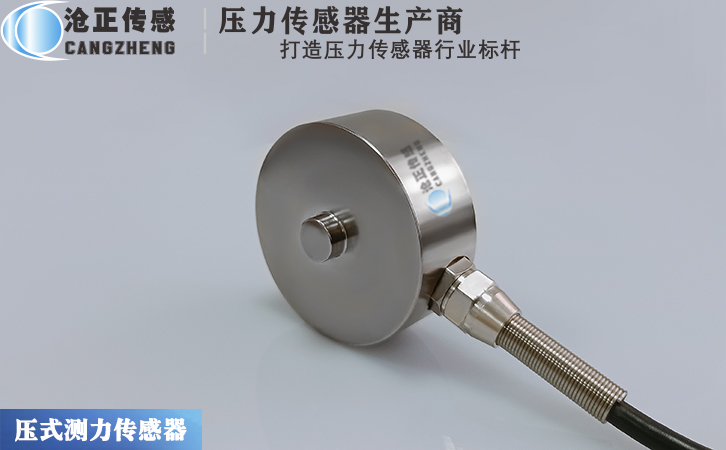
一、影響測力傳感器壽命的主要因素
材料與設計
彈性體抗疲勞性:合金鋼或不銹鋼的疲勞壽命可達數百萬次循環,劣質材料易因應力集中導致裂紋。
應變片與粘合劑:高性能應變片(如金屬箔式)壽命可達10?次動態加載,劣質粘合劑易老化失效。
密封等級:IP67/IP68防護可避免濕氣侵入,未密封傳感器在潮濕環境中壽命可能縮短50%以上。
負載特性
靜態負載:長期滿量程靜態壓力可能引發蠕變(如鋁合金彈性體蠕變率>0.1%/年)。
動態負載:高頻沖擊或過載(如超出150%額定負載)會加速疲勞,典型工業測力傳感器動態壽命為1×10?~1×10?次循環。
偏載/側向力:非軸向力導致局部應力超標,可能使壽命降低至設計值的30%以下。
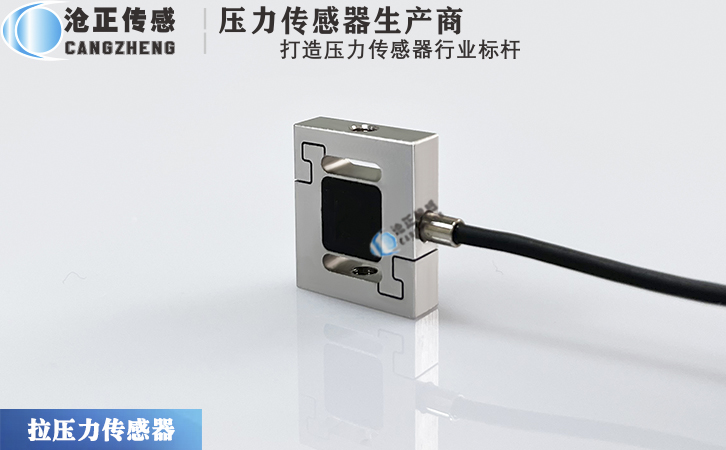
環境條件
溫度:長期在>80℃環境使用,有機粘合劑可能碳化,導致應變片脫粘。
腐蝕性介質:鹽霧或酸性氣體環境下,未防護的測力傳感器壽命可能不足5年。
振動與沖擊:無緩沖安裝時,高頻振動(>1kHz)易引發機械共振,導致結構斷裂。
電路穩定性
供電電壓波動(>±5%)或EMI干擾可能使信號調理電路元件(如運放、ADC)壽命縮短。
二、典型應用場景下的壽命范圍
應用場景 | 負載類型 | 典型壽命 | 失效模式 |
---|---|---|---|
實驗室靜態稱重 | 靜態、低頻率 | 10~20年 | 零點漂移、蠕變累積誤差 |
工業自動化生產線 | 動態、中高頻 | 5~10年(或1×10?次循環) | 應變片斷裂、彈性體疲勞裂紋 |
工程機械(起重機) | 沖擊、高負載波動 | 3~7年 | 過載導致塑性變形、密封失效 |
海洋平臺監測 | 腐蝕性環境 | 5~8年(需定期維護) | 外殼腐蝕、電路短路 |
三、延長使用壽命的關鍵措施
選型優化
選型優化
選擇額定負載1.5倍于實際最大負載的測力傳感器(如實際負載1000N,選1500N型號)。
動態應用優先選疲勞壽命≥1×10?次循環的型號,并標注動態安全系數(如FS≥200%)。
安裝與保護
使用萬向節或自對準底座消除偏載,側向力需<5%額定負載。
沖擊場景加裝液壓緩沖器或橡膠墊,將沖擊加速度限制在<10g。
高溫環境增加散熱片或隔熱,確保壓力傳感器溫度<規格書限值(通常-20℃~+80℃)。
維護與監測
定期校準:靜態應用每12個月校準一次,動態應用每6個月校準。
清潔與檢查:每季度清理傳感器表面積塵,檢查電纜接頭是否氧化。
數據趨勢分析:通過監測零點輸出(如漂移>0.1%FS/月)預警潛在故障。
環境控制
濕度>60%時啟用氮氣吹掃或干燥劑保護。
腐蝕性環境使用哈氏合金外殼或噴涂特氟龍涂層。
四、失效征兆與更換判斷
電氣性能異常
零點輸出漂移>0.5%FS(空載時輸出偏離初始值)。
橋路電阻變化>0.1Ω(正常應變片橋阻通常350Ω±0.5Ω)。
機械損傷
彈性體可見裂紋或塑性變形(使用內窺鏡檢測隱蔽部位)。
密封圈老化導致IP等級下降(如內部結露)。
功能失效
重復性誤差>0.05%FS(同一負載多次測量偏差過大)。
非線性度超標(如標定曲線偏離理想直線>0.1%FS)。
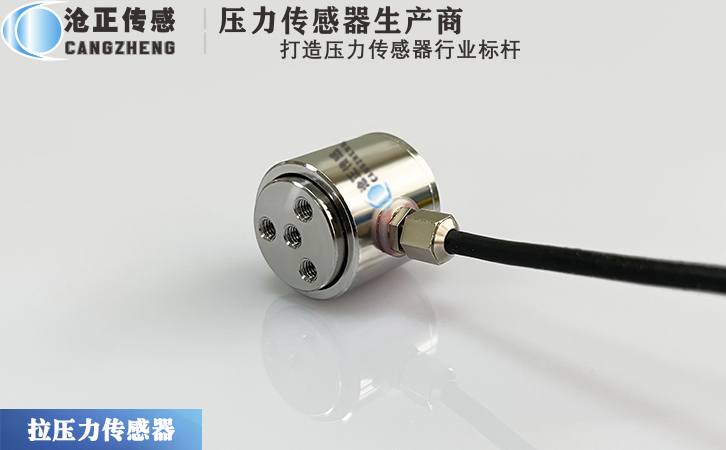
測力傳感器的使用壽命可通過科學選型、規范安裝、環境控制及預防性維護顯著延長。工業級傳感器在典型工況下通??煞€定工作5~15年,而實驗室高精度傳感器在理想條件下甚至可達20年以上。關鍵是通過系統性管理,使實際壽命接近設計理論值。